When your motor is in need of rewinding, you need to find a company that specializes in this service. This article will cover the cost of motor rewinding, signs that your motor needs rewinding, and common problems associated with the process. Then, we’ll explain some of the alternatives to rewinding. If you’re still not sure that you need DC Motor Rewinding, read on to learn about your options.
Cost of Rewinding a Motor
The cost of rewinding a DC motor is about 40% less than buying a new unit. For thrifty companies, rewinding a motor can save them a lot of money. It is possible to rewind small, fan-cooled motors up to 100 horsepower, although some types of motors can’t be rewound. Some types of motors are too damaged to be rebuilt, such as those with cracked laminations and damaged magnetic cores. In addition, rewinding may not be suitable for motors with bearing failure or damaged laminations.
Despite the high cost of rewinding a DC motor, this process is relatively easy. It can save you a lot of winding, and you can save money on the process by repairing the motor’s housing. However, it can be more expensive than other types of repair, such as reconditioning or housing repair. So, be sure to compare costs before deciding to rewind a motor.
Signs That a Motor Needs Rewinding
Rewinding a motor can be done for several reasons. It can fix problems caused by excessive wear and tear and improve efficiency. When a motor starts showing signs of inefficiency, it is time to consider rewinding. This process involves rewinding the armature to regain the motor’s efficiency and strength. Here are a few signs your motor might need rewinding.
Burn marks on the windings of the motor are a sign that it’s time to get it rewinded. Old motors often have charred insulation and burned windings can cause the motor to operate intermittently with reduced power for years. To determine if the motor needs to be rewinded, check its insulation for burnt wire. If this is the case, you can start the rewinding process and save money in the long run.
Problems Associated With Rewinding
There are some common problems associated with DC Motor Armature re-winding. If you experience any of these problems, you should consider rewinding your motor to restore its optimal performance. During re-winding, you should be sure to record all measurements and problems, so you can track and troubleshoot problems as they arise. Listed below are the most common issues.
Open Winding: Open winding can be caused by various factors, including undersized lead lugs, charred connections on the motor connection box, and phase-to-phase and ground-to-frame shorts. Physical damage to the coils can also cause open windings, and this will require rewinding or replacement of the motor. If you suspect that your armature requires re-winding, follow these simple steps to ensure its optimal performance.
Alternatives to Rewinding a Motor
If your dc motor is failing, you have probably considered rewinding it. This process involves reversing the direction of the electric current that runs through the armature. To do this, you will need to remove the armature. Once you’ve done this, you will want to check the resistance on the motor windings. The resistance will depend on the voltage of the motor and the size of the conductors in each coil. If the resistance is drastically different for one measurement, you probably have a problem with the windings. Likewise, if the resistance decreases suddenly, you likely have burned a wire.
Another alternative to rewinding a motor – rewinding a single winding is enough to repair a motor with burned wires. A wooden template works well for this process as the paper reaches the metal tabs surrounding the brush pads. The wires should be as long as the first winding. The rewinding process should take around two hours. In addition to rewinding the armature, this technique can be very useful when you have a limited time or are unfamiliar with the process. Visit ghaimagroup.com for more.
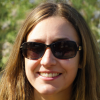
Tropical swift lover.